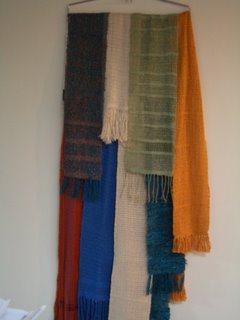
I realized I was amiss for not discussing bead leno...I had a three day compulsive period where all I did was warp and weave bead leno.
It all started with a workshop by
Robyn Spady called the
Fab 4 - unleashing the power in your four harness loom. The workshop was fabulous...if you ever have the opportunity to take one of Robyn's seminars or workshops - you will not be disappointed. We had about 12 weavers in our workshop from novice all the way through advanced. Everyone got lots out of the workshop.
The workshop was in a round robin format and we got to weave ten different structures. One of the looms I brought had bead leno warped on it. It's a simple 1-2-3-4 sley job which needs to be done initially back to front. Before putting the yarn through the reed, one gathers the yarn in sets of four. Then you take 1 & 4 together through a craft bead and then take all four through one dent in the reed. The bead causes an automatic twist in the yarn when certain shafts are raised and creates a lacy effect.
For some reason I found the
bead leno weave structure quite intriguing. It is supposed to be useful to use with novelty yarns since you don't have to use too much. It looks lacy without knitting or crocheting. I liked the result regardless of what yarn I used - the silk feels great, the perle cotton looks great and the novelty yarns are quite unique. A true test: I like them enough that I actually wear them! The only downside is that with all lacey creations - things get caught in them...like little dog nails. And there are lots of those in our house. Fortunately, it's pretty easy to pull the scarf back in shape.
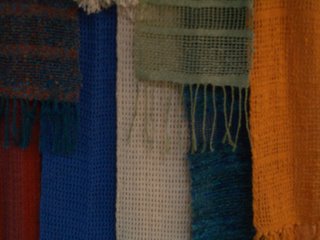
They were fast to create...I had a real production line going. Since the loom was already threaded, I was able to tie on warps real quick using the front to back method. I didn't even use a warping board. Simply put two C clamps the right distance apart and measured out the warp in three sections. No cross and no mess! I tried it with silk, perle cotton and linen warp. Quick and easy.
I was able to warp and weave a scarf in less than three hours. I completed eight scarves in three days and I like them all. Yes, I was compulsive. But I think bead leno is now out of my system....