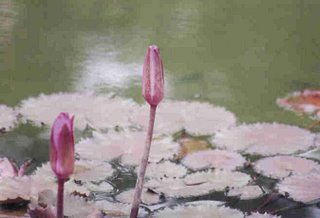
Here is a little story about my first experience weaving on a TC-1.
This is quite the ultimate loom - no limitations on design due to the number of shafts. Each heddle moves on its own. There seemed to be thousands of them! How cool!
I took a class called Color Optimization at Convergence this year. It was quite fun. We started with a photo. I took this one in China and it has been one of my favorites. I already did one tapestry of this scene. We played around with the photo in Photoshop to get to the right resolution. We also spent some time changing some of the pixels so we would not have long warp or weft floats on the front or back of the final weaving.
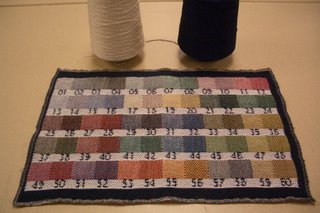
The loom we were using was a TC-1 from Norway which was warped with six colors of warp in a repeating format. The warp colors were white, black, yellow, green, blue and red. By selecting a dark, a light and a grey weft and through the magic of color optimization we were able to fool the eye so from six colors we ended up with a palette of 60 colors for our weaving. Here is a photo of the palette if one used black and white as the dark and light weft colors. You can see the colors do have varying hints of darkness...
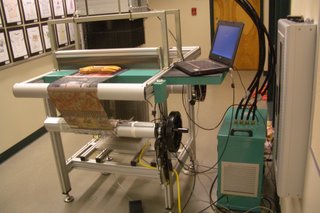
Here is the loom with my weaving ready to go. You can see it has a computer assist - obviously. Just look at all those individual heddles which move separately from each other. The heddles are about three feet long. The green box on the right is an air compressor which lifts the selected heddles and makes the shed. There is a beater that you pull by hand like on a normal floor loom. There is a foot pedal on the floor to move along to the next shed. I found the pedal quite uncomfortable to use - it bothered my foot. It might have been easier with a bench or at a different angle.
I must admit that I find this loom somewhat odd...with all this technology one still has to push a pedal to make a shed, beat by hand and throw three shuttles to weave. Why not automate the entire process? It certainly seems like the real value of this process is the able to design anything you might want without being constricted by the number of shafts. Why even throw the shuttles and beat? Perhaps in the next generation....

Here is my selection of wefts. I chose an off white and a dark green as my light and dark weft colors. And a thin grey as my binder weft. We saw a number of examples of pieces at the beginning of class and I felt they were way too dark and somber for my taste so I wanted to see if I could get a light airy look for my piece. This is a good picture to see the varied colored warp. Since my piece has a lot of reds and greens that's why those warp colors are near the top. The colors I don't use are underneath. You can just see where the lilly flower is starting to show.
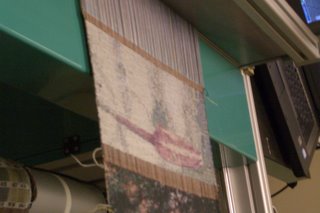
Here is the finished piece. It is an interesting technique to use.
We learned how to do something similar on an eight harness loom...getting a 24 color palette from a four color warp. I may try experimenting with this to see what I can do...
No comments:
Post a Comment